|
Our first case history
is a well with a Rotoflex 1100 pumping unit with a 306” stroke
length.
The 2’ bore pump is set at 8900 feet. The Cardbuild® System was installed In January of 2009. Prior to that time the
well was running approximately 3.5 SPM with a conventional VFD
system and was producing 380 BGPD. Prior history indicated about
3 failures per year that required a rig. These included tubing
leaks, rod parts and pump changes. Some of these issues
continued to be worked through after the Cardbuild®
System was installed. As existing problems were eliminated the
rig frequency decreased significantly. The last rig job was
3/29/2010. When the well was put back into operation after that
date, it ran approximately 5 SPM with a production test rate of
540 BGPD. It ran this way until January
2014 when it was replaced with a pumping unit with a 366” stroke
length. In the four years after the pre-existing problems were
cleared up, it required only routine maintenance work. It never
experienced a mechanical failure that required a rig or an
extensive shut down period. During this period, there were over
9,000,000 pump strokes and total fluid lifted was approximately
700,000 barrels.
Conclusion:
After
installation of the Cardbuild® System this well has consistently
operated at higher stroke speed which has increased well
displacement by approximately 40%. At the same time, equipment
failures, both surface and down hole, have dropped substantially.
Net results" |
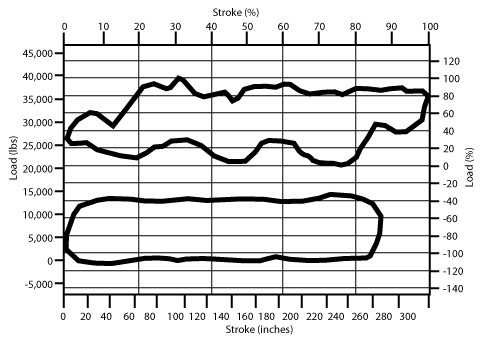 |
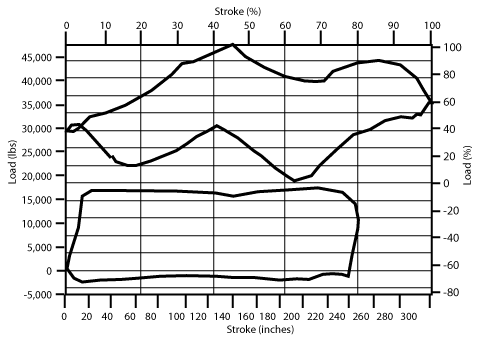 |
Conventional System |
CardBuild System |
|
|